Pro Tips for Working With Pottery Glaze
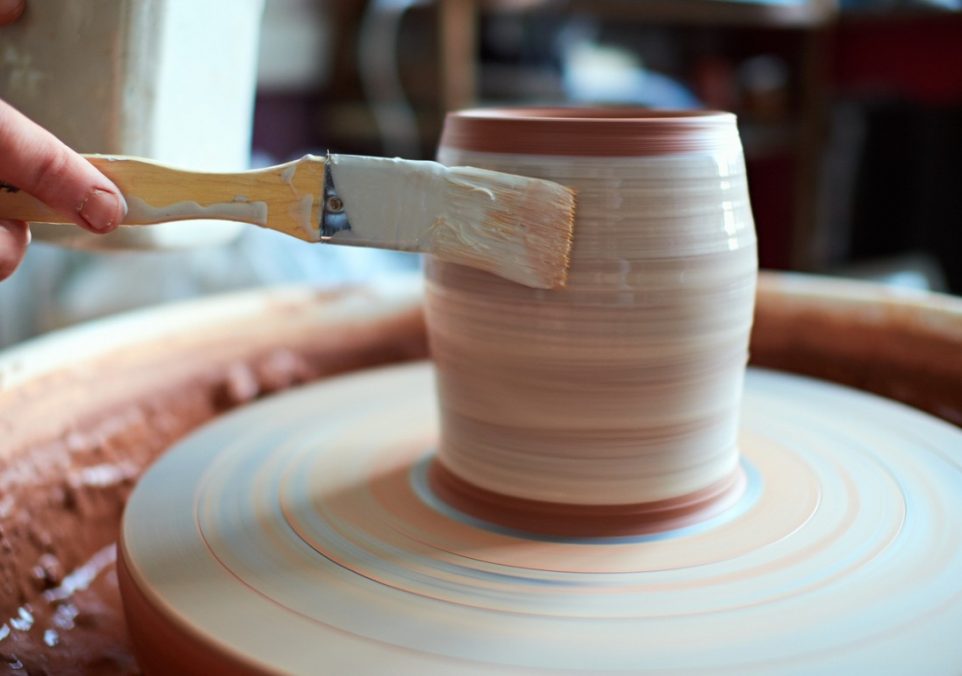
Pottery is a creative and therapeutic art form. Working with pottery glaze can be tricky, but with the right tips, you can create beautiful, long-lasting pieces of pottery. In this post, we’ll discuss the most effective techniques for working with pottery glaze and provide pro tips to help you create stunning art pieces. We’ll cover everything from the proper glazing techniques to tricks for achieving the perfect finish.
Whether you’re new to pottery or an experienced artist, you’ll find something helpful in this article. We’ll show you the basic tools you need, the different types of glazes, and how to pick the right glaze for your project. With these tips, you’ll be equipped to achieve stunning results that will last for years.
Types of Glaze
The clay body is the base material that will be used to form your pottery piece. First, select a type of clay best suited for your project and your desired look. To help decide, research different types of clay and what kinds of artwork they’re useful for creating.
Once you’ve chosen a clay body, you’ll need to select a glaze. The type of glaze you use depends on your desired result and the look or theme you’re trying to create. There are two types of glazes available: leadless and lead-based glazes.
Leadless Glazes
Leadless glazes are often used in low-fire pottery because they are less expensive than their lead-containing counterparts, require fewer health and safety precautions, and don’t contain hazardous materials that can be harmful. Leadless glazes may not be as durable as those containing lead, however, because they require a lower firing temperature.
Lead-Based Glazes
Lead-based glazes are higher in quality than their leadless counterparts and are good for stoneware and earthenware pieces that require high-fire temperatures. Lead-based glazes also have greater color variability than leadless ones, making them a popular choice among potters who want more control over the look of their pottery pieces.
Preparation
Once you’ve selected the clay body and type of glaze you’re working with, it’s time to prepare for application. Before adding any glaze to your clay body, ensure it is clean and free of debris or dust particles that may interfere with the smooth applied finish you want. Thoroughly rinse the clay body in warm water while gently rubbing away any dirt or foreign particles with a soft cloth or sponge before continuing with the other steps.
Testing your chosen clay body and glaze combination is essential before you begin to apply the glaze, as not all combinations will work together successfully during the firing processes. Prepare small test tiles using your chosen material and fire them to check compatibility under various conditions, such as firing temperature and duration, before starting a full-piece project with your chosen combination of clay body and glaze material.
Mix your chosen materials according to manufacturer instructions for the best possible result during the application and firing processes. This may include stirring the glaze for an adequate amount of time and adding any additives necessary for greater success, such as plasticizers and fluxes. Make sure to mix up only what you need, as the extra mixture can cause problems during application if not handled properly due to drying times once exposed to air.
Application
After cleaning and testing your clay body and preparing the mix according to instructions, it’s time to apply the glaze to your piece using the optimal techniques for your project. There are three popular techniques that you can use: dipping, spraying, and brushing.
Dipping
Dipping involves submerging the entire piece or selected sections into prepared mixes or washes. This can be done using plastic or rubber coats or by pouring trained aluminosilicate or rutile slips onto the piece. The aim is to create special effects or detailing, depending on the artist’s preferences. Dipping techniques cover large sections simultaneously, with even coverage from uniform depths, to achieve the desired results for the project piece.
Spraying
Spraying involves using specialized nozzles to spray prepared mixes or washes onto the piece. Depending on the sprayer used, this technique also aims to create special effects or detailing. Spraying covers large sections at once, with controlled levels of coverage based on distance, to achieve the desired results for the project piece.
Brushing
Brushing involves using a brush to apply prepared mixes or washes onto the piece. This technique covers small sections at once, with various levels of coverage depending on pressure and the brush type used. Brushing is also used to create special effects or detailing based on the artist’s preferences and desired results for the project piece.
Firing
After completing the application stage, the next step is firing the project piece based on cone range and firing time and using either bisque-firing or glaze-firing. The firing method chosen depends on the artist’s desired results, such as color range and clarity.
Both cone range and firing time must be considered when firing a project piece. The cone range refers to the temperature at which the piece will be fired. Different cone ranges, such as cone six oxide stoneware versus low-fire earthenware, can affect colors. The correct kiln size is also essential to ensure successful firings.
Bisque-Firing
Bisque-firing involves preheating raw clays before applying glaze material. This process removes any gases released by plastic clays, which could interfere with the finished product’s appearance when fired at higher temperatures. The rate of preheating depends on the size and weight of the project piece, while the kiln size used affects the success of the process.
Glaze-Firing
Glaze-firing involves heating already bisque-fired pieces to further temperatures until peak maturity levels, determined by specific cone ranges according to the artist’s needs and project goals. Unlike bisque firings, which level off earlier due to the higher temperatures required, glaze firings occur until peak temperatures are achieved within a specific time frame.
Troubleshooting
Experienced potters may be aware of problems that can arise during firings, such as bloating, cracking, and spotting. To troubleshoot these issues, it’s important to understand their causes.
Bloating
Bloating occurs when gases build up inside the kiln chamber due to incorrect kiln sizes or trays loaded inside. This can lead to cracking, especially in hot spot areas, caused by air gaps against wall elements inside the kiln. To avoid this, it’s important to use the correct size trays in kilns.
Cracking
Cracking can occur due to improper preparation of application mixes or improper handling, such as sudden temperature changes. This causes tension between trays and pots inside the kiln, creating pressure points against walls and resulting in cracking effects after firing.
Spotting
Spotting can happen due to dust spots left behind from prior cleaning before introducing trays into the kiln chamber. These can create hot spots that appear in undesired spots on the pottery after firing.
Finishing
After firing and cooling, the next step is finishing the pottery piece. This involves refining the surface by removing any remaining dirt or debris using gentle brushes. Special care should be taken to protect the edges of the pottery as they may be softer due to previous finishing processes.
The next step is sealing and waxing the surfaces of the pottery piece to protect it from damage. Specialized sealing waxes are used to apply a protective coat around the edges of the pottery piece.
Finally, any cracks or chips in the pottery piece can be repaired using specialized plaster products. Cracking issues may occur due to improper material combinations or mishandling during the composite creation process, so it is important to use proper techniques and tools to avoid potential damage.
Trusted Insights from Artists
At Art Life Today, our passion for arts and crafts is at the heart of everything we do. We understand that the right tools and materials can make all the difference in your creative projects, so we take our responsibility as reviewers seriously. Our goal is to help you discover the best products that will inspire your creativity and bring your artistic visions to life.