Plaster, Rubber, Resin: What Material is Best for a Casting Mold?
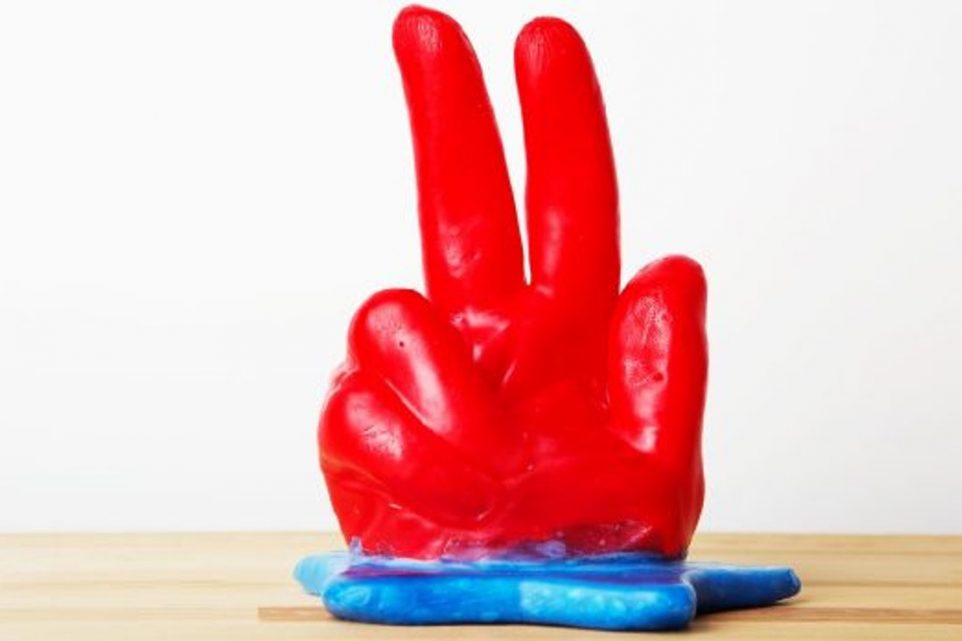
Casting is an art form that has been around for centuries and is used to create a variety of objects, from sculpture to jewelry and more. Finding the right material to use for your casting project can be a challenging task, especially for those who are just beginning their journey into this wonderful world. In this post, we’ll discuss the different materials that are used for casting and what to consider while using them.
We’ll cover a variety of materials, from traditional casting metals (like bronze and iron) to modern alternatives (like silicone and resin). We’ll also discuss the pros and cons of each material so that you can make an informed decision on which one is right for you. So, if you’re ready to start your casting journey, let’s get started!
Types of Casting
The process of casting involves pouring melted material into a mold or die to create a three-dimensional object. The traditional foundry casting process is still in use today, although it’s mainly used for larger objects in large-scale production. Sand casting is another popular technique involving making sand molds out of oil or resin-bonded sand. Investment casting, on the other hand, is a process characterized by the use of a wax pattern surrounded by a ceramic shell to obtain an accurate shape and finish.
Materials Used
Metals are some of the most commonly used materials for casting, particularly those with low melting points, such as aluminum and zinc. Metals like iron, steel, brass, bronze, and lead can also be cast, but they require the use of more advanced equipment and materials. Plastics are also commonly used for casting due to their versatility and low cost, and wax is often used in combination with other materials to create intricate parts through investment casting techniques.
Important Considerations
The first thing to consider when choosing any casting material is its cost. Metals tend to be more expensive than plastics, either due to material costs or production costs associated with the specialized equipment needed to cast them. Depending on the size and complexity of the part being made, certain processes may be more suitable than others due to the limitations imposed by certain techniques (such as patternmaking) or shrinkage factors after cooling. Additionally, design requirements (such as how many parts need to be created or the level of detail necessary) must also be considered before selecting which process to use for hand-casting something from scratch.
Specialty Processes
Vacuum casting makes use of silicone molds rather than metal or plastic ones and allows parts to be quickly and accurately replicated in high volumes at a relatively low cost. Lost foam casting works similarly, but it instead uses polystyrene foam as the pattern. This is then burned away, leaving behind only the hollow cavity to be filled with molten material. With 3D printing technology becoming more common and affordable these days, this technique is increasingly being used to produce one-off parts with excellent detail and accuracy.
Casting Defects
Several common defects can occur during the casting process, and these can be due to improper material selection or temperature variations during solidification. These include things like porosity, misruns, and shrinkage, but by taking care to avoid them, you can enjoy high-quality castings no matter which kind of material you’re working with.
Finishing Steps
Once a part has been successfully produced through any of these processes, there are still several steps that should be undertaken before it’s ready to be used or displayed. Surface finishing typically involves polishing or buffing, while heat treatment might also be required depending on the metal being cast. Machining may also be needed in some cases, like when complicated components need precision parts that cannot be made using other methods, such as extrusion or injection molding.
In summary, the materials you use while casting can play an important role when it comes to creating your finished product. With this in mind, make sure you consider all your options carefully regarding cost-effectiveness and design requirements before proceeding with any given project or purchasing a hand-casting kit. Once you’ve gone through all these steps, you’ll likely have a beautiful object ready for final assembly and display!
Trusted Insights from Artists
At Art Life Today, our passion for arts and crafts is at the heart of everything we do. We understand that the right tools and materials can make all the difference in your creative projects, so we take our responsibility as reviewers seriously. Our goal is to help you discover the best products that will inspire your creativity and bring your artistic visions to life.